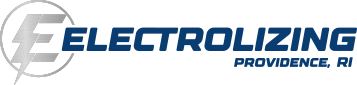
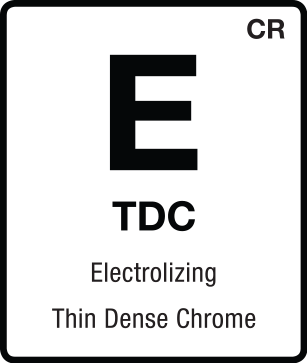
THE ORIGINAL THIN DENSE CHROME SINCE 1945
FOR OVER 77 YEARS WE HAVE CONTINUALLY REFINED OUR PROCESS TO KEEP IT THE MOST ADVANCED, ULTRA PURE AND VERSATILE THIN DENSE CHROME AVAILABLE ON THE MARKET.
BY ADDING DURABILTY AND ENHANCING PERFORMANCE, THE ELECTROLIZING COATINGS ARE DESIGNED TO KEEP YOUR PARTS, TOOLS AND EQUIPMENT UP AND RUNNING.
CALL OR EMAIL US TODAY TO DISCUSS AN ENGINEERED SOLUTION THAT’S CUSTOM TAILORED TO YOUR INDUSTRIAL APPLICATION.
1-401-861-5900
20 Houghton St.
Providence, RI 02904-1014
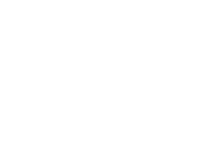
Wear
< 1.2 TWI per AMS 2438
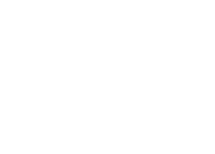
Hardness
Up to 72Rc
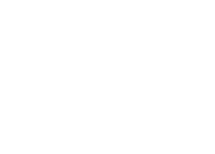
Corrosion
ASTM-B-117 Compliant
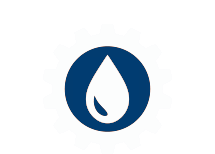
Lubricity
As low as .09 CoF

Galling
Eliminate cold welding
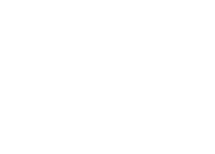
Adhesion
Atomic, absolute
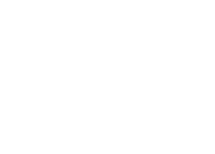
Appearance
Gray Satin
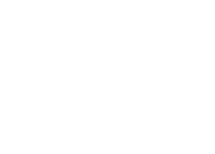
Deposit
.000050”-.0001”
OUR HISTORY
Developed in 1945 in Providence, RI, Electrolizing® is the originator of thin dense chrome (TDC) technology. For over 77 years we have consistently refined our process to keep it the most advanced, ultra-pure, and versatile thin dense chrome coating available in the market.
The Electrolizing® TDC coating continues to be the gold standard of coating technologies for industrial applications.
ELECTROLIZING® COATING FEATURES
The Electrolizing® thin dense chrome coating increases wear resistance and performs at <1.2 TWI per AMS 2438. In addition the coating is ASTM-B-117 compliant and provides prolonged corrosion protection even when compared to stainless steel.
Electrolizing® has a hardness rating of 70-72 on the Rockwell C scale with lubricity as low as 0.09 CoF. This very low surface friction makes it ideal for surface-to-surface contact of moving parts.
The Electrolizing® coating acts as a dry lubricant which prevents galling and the need for cold welding. It has proven to be an excellent application for threaded components.
Absolute adhesion is also achieved when applying Electrolizing® thin dense chrome, meaning the coating will not chip, flake or peel. The appearance of the coating is a gray satin finish, with a deposit thickness of 0.00005-0.0001”.
ENGINEERED FOR PERFECTION
The Electrolizing® coating is a proprietary blend of pure chromium that produces a very hard surface. The coating is applied at a temperature below 180 degree F. This cold process protects precision-machined parts from distortion or annealing.
Engineered TDC deposits can be applied from 0.00005″ to 0.0001″ per surface according to customer specifications. Precision tolerance requirements can be engineered for each individual application.
The Electrolizing® coating has a smooth, fine-grained surface and will be free of blisters, nodules, porosity, and the potential for edge build-up.
ELECTROLIZING® COATING APPLICATIONS
The Electrolizing® coating is used across a wide variety of industries including plastic injection molding, food processing, oil and gas, aerospace, medical, and nuclear power. The metals that can be treated with this coating include:
- Aircraft Steel
- CRS
- Aluminum
- Stainless Steel
- Brass
- Tool Steel
- Bronze
- Inconel
- Beryllium Copper
- Monel
- Copper
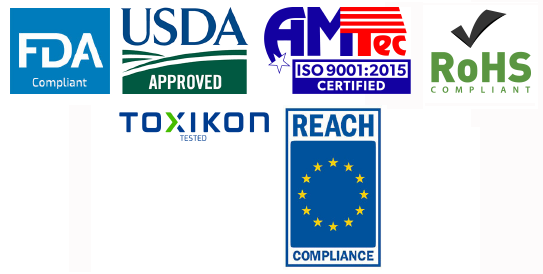
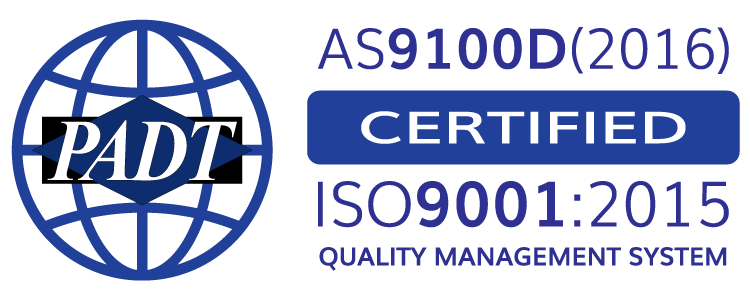
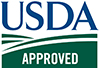
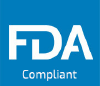
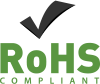
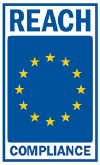
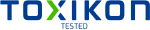